Coca-Cola Europacific and FlexBlow: Bringing Hot-Fill Bottle Production to Fiji
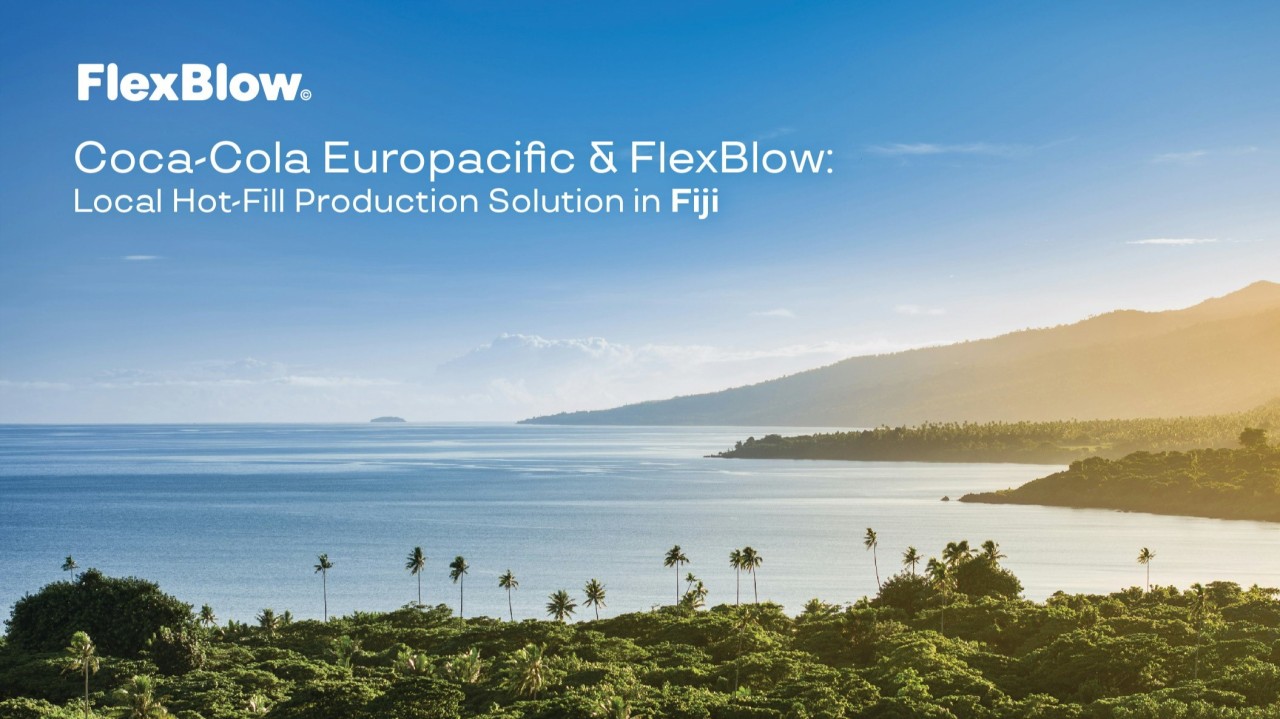
Bringing Hot-fill Bottles Production Inhouse
Sustainability is a global priority, but for businesses operating in remote locations like Fiji, it’s much harder at the same time more crucial to do. Manufacturing in tropical climates presents unique challenges—high temperatures and humidity can affect machinery performance, requiring innovative solutions to maintain efficiency and product quality.
One of Coca-Cola Europacific’s biggest challenges in Fiji was producing hot-fill bottles locally. Hot-fill packaging, commonly used for non-carbonated beverages like juices, energy drinks, and sports drinks, requires precise temperature control to ensure stable production, product safety and shelf stability. In a tropical climate, this process demands specialized equipment that can handle heat and humidity efficiently.
Previously, Coca-Cola Europacific relied on imported empty bottles from Australia, leading to high logistics costs and high CO2 emissions. With growing demand in Fiji, the company sought a sustainable and cost-effective solution to stabilize supply and reduce environmental impact.
Partnering with FlexBlow for Innovation and Flexibility
Coca-Cola Europacific first explored FlexBlow’s technology at the 2022 Drinktec exhibition. What stood out was FlexBlow’s highest flexibility and innovations combined with fastest changeovers in the market. Additionally, company presence in the Oceania region provided confidence in the reliability of the machinery.
The major step toward finalizing local hot-fill bottle production was made in July 2024, when the FlexBlow 4 model was installed. The machine started producing the full range of hot-fill bottles, with the capability to manufacture hot-fill bottles starting as low as 20 milliliters and up to 6 liters
As one of the world’s largest bottling corporations, Coca-Cola Europacific sets high-quality and safety standards that not all manufacturers can meet. FlexBlow’s ability to deliver precision, flexibility, and efficiency made it the perfect partner for this project. Its technology was specifically designed to operate under Fiji’s tropical conditions, ensuring smooth and reliable production.
The Impact: Lower Costs, Less CO2, and Greater Control
Transitioning from imported bottles to in-house production has delivered significant benefits for Coca-Cola Europacific. Instead of shipping bulky empty bottles from Australia, the company now transports preforms, allowing up to 10 times more units per shipment. This shift drastically reduces logistics costs per piece and cuts carbon emissions.
Local production also gives Coca-Cola Europacific greater control over quality and faster response times to market needs. By reducing reliance on imports, the company can ensure a more stable supply chain while advancing its sustainability goals.
A Model for the Future
The success of this project in Fiji proves that local production can overcome the challenges of remote locations. Coca-Cola Europacific is now looking at expanding this model to other regions, further reducing emissions and increasing flexibility.
This partnership with FlexBlow highlights how innovation and sustainability go hand in hand—creating a greener, more efficient future.
Is your business facing similar challenges in bottle production? Let’s talk about how FlexBlow’s innovative solutions can help you achieve greater efficiency, sustainability, and flexibility—no matter the location. Your success story could be next!